Scientists in the US have folded a nanoscale wafer of aluminium oxide, with a pattern of gold on its surface, into a hollow cube, creating a tiny optoelectronic device. They have made the smallest ever 3D split-ring resonator, a device widely used in new metamaterials that have unusual physical and electronic properties.
The researchers say that the 3D device is more active than its 2D counterpart, and that the work demonstrates the feasibility of creating functional, precisely engineered devices at the nanoscale.
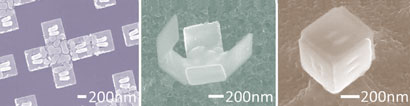
David Gracias and colleagues at Johns Hopkins University in the US showed previously how nanoscale origami could be used to fold a sheet into a cube. They have now taken the process a step further by functionalising the product.
To make the cube the team first deposits a layer of polymethylmethacrylate on to a silicon substrate. They then use electron beam lithography to carve out a mould into a cruciform shape consisting of the six sides of the final cube. The mould is filled with aluminium oxide. A second layer of polymer is deposited and portions etched out at the meeting point of the individual panels, where tin is laid down to form the hinges for the box. The polymer is then removed and the silicon etched away with activated fluorine. This process is exothermic, and the heat generated melts the tin. As the molten tin coalesces it creates twisting forces that cause the alumina panels to fold inwards, creating the cube.
The team put gold on to the surface in the pattern for a split-ring resonator before overlaying the cube's panels to create the optoelectronic properties.
'In nanotechnology, it is relatively easy to make particles, but introducing patterning is less straightforward,' says Gracias. 'Here we have shown that we can engineer precise geometries and introduce patterns which have function.'
Mark Morrison, chief executive of UK educational charity the Institute of Nanotechnology, says that the combination of top down lithography and deposition and bottom up self assembly methods is of 'particular interest'. The devices, he adds, could have applications in a range of fields from computing to medicine. 'This is clearly cutting edge, fundamental research which still needs a lot of development before it could find real life applications,' says Morrison. 'One major issue will be scaling up this technology to manufacturing levels.'
Gracias says that the process has limitations. 'It is expensive, and we can only make a few structures at a time. But what we are doing is pushing the limits of this type of engineering.'
Simon Hadlington
References